Natural
In’novation
Valco Group
History and Passion are the guidelines conveyed by generations of employees.
Just like Nature, Valco Group has been building up its organic structure from the roots, fueled by the know-how of its human resources in order to reach the very top of the tree, and reason of our continuous growth: our customers.
All this has made it possible to offer functional and decorative solutions which combine passion to close respect for the environment.
Natural In´novation
OUR HISTORY
Since 1958…
1958
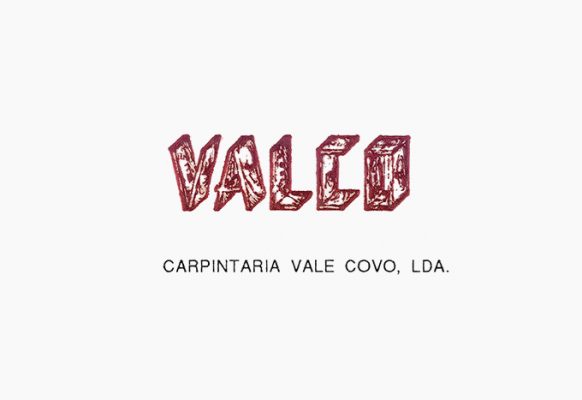
Start-Up
The company, formerly called “Carpintaria Vale Covo, was founded in 1958 and has started production in March. 1958, in a narrow 80sqm hall, set up by its own founders.
It was officially registered on May 2nd, 1958, with 3 partners, Mr. Gabriel Oliveira being its leader.
1958
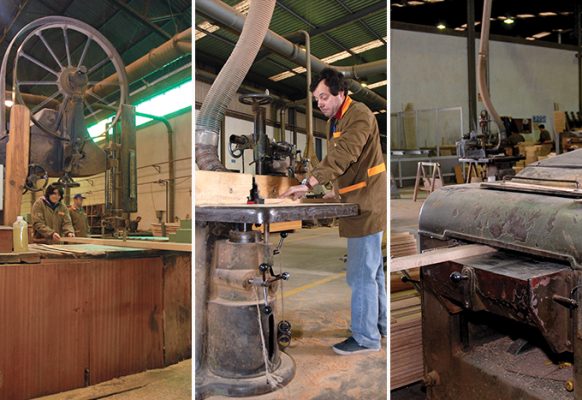
First wood-working machines
By mid-1958 the company was already equipped with some new machinery and employing:
1 plane, 1 router operator, 4 carpenters, 5 trainees, as a result of the investment in the first equipments: a mechanical plane, a router, a table saw and a circular saw.
1958
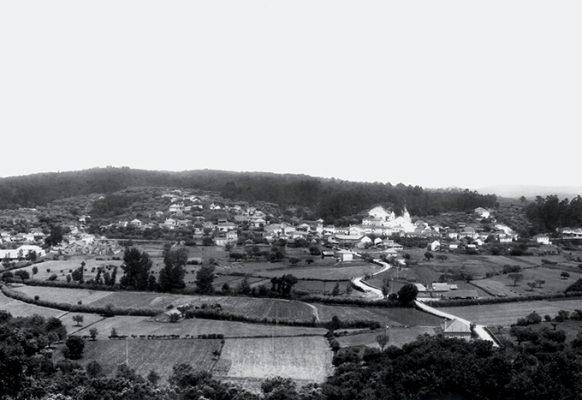
Growth
By those days, Lisbon was noticing a fast development with plenty of new housing projects on the ground, so the number of our employees gradually increased as well.
With the increasing number of employees, an air siren has been installed in order to warn workers of opening, lunch time and closing times of the factory. Even today its sound remains a distinctive and peculiar one that traces the rhythm of everyday’s social life around the village of Caranguejeira.
1969
More than 50 employees
By the end of the 1960’s, Manuel Rodrigues, one of the stakeholders, left the company. At the time, Valco was already employing more than 50 workers and the facilities surfaced around 200m2.
1972
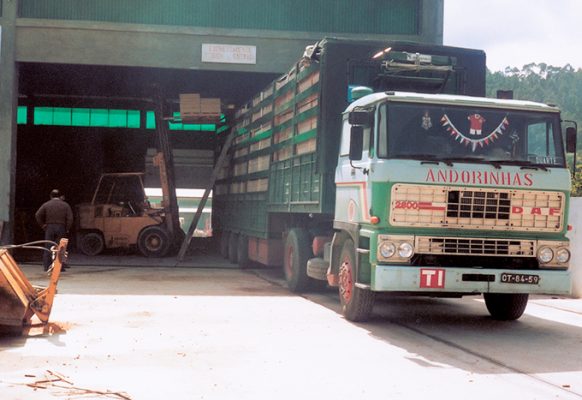
Exports
The beginning of exports to France and Germany made it necessary to hire a professional interpreter, invest on a new truck for long trips and to purchase office support equipment in Lisbon. Trade relations with foreign markets and the presence in international trade fairs reinforced the need for new equipment, in order to be able to follow modern market trends and updated technologies. The investment on a first press line for flush doors has enabled us produce around 50 units per day!
1972
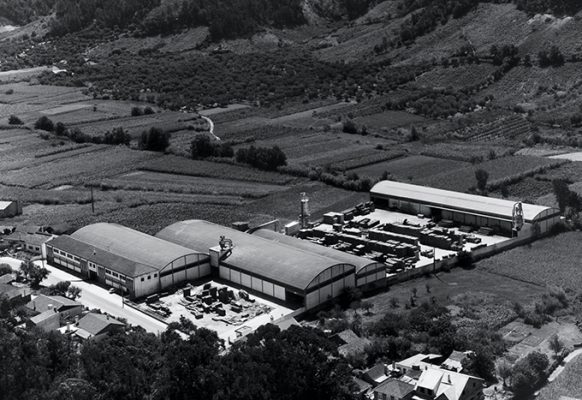
The 1970’s
The 1970’s saw a rapid growth of the company and larger scale investments like:
first Kiln-dryer, lacquer finishing line as well as an automated accounting system.
Ten more employees were hired by the time.
1974
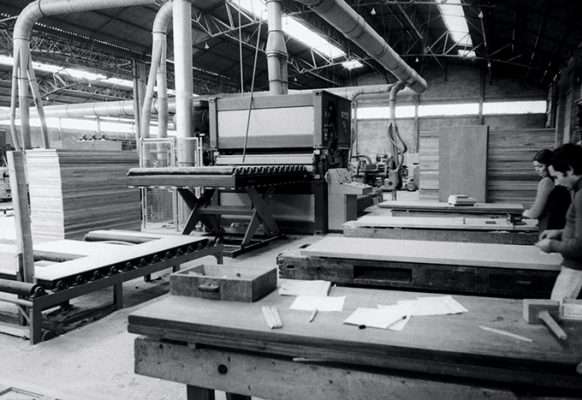
April Revolution, 1974
Unstable political situation the country faced as a result of the april military coup in 1974, created a serious impact on the overall domestic economy and most critical in the building sector when many housing projects were cancelled or even abandoned. Once again, the directors of Valco showed strong human concern with the well-being of employees and all jobs were kept for everyone, without any salary delays or strikes. Due to a sharp shortage of regular orders, and the need to keep the factory running, production had then to turn to the manufacture of quite unusual items like: barrels, oxen carts, and many other wooden farm tools that could be used by local farmers.
1979
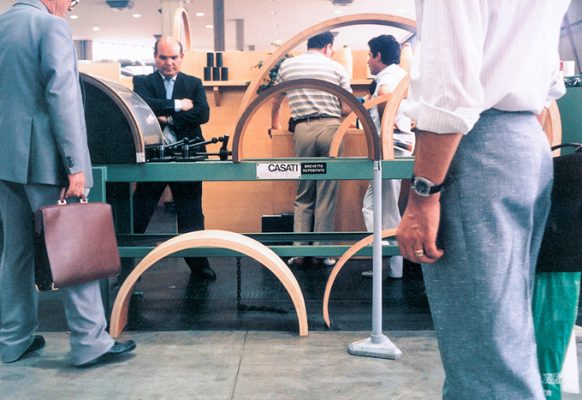
Social and economic stabilization
By the end of the 70’s, when the country finally stabilized and life went back to normal, many projects were revived and construction sector saw an upward move, with major jobs being concluded, such as: School of Mexia in Montemor-o-Novo, the German military camp in Beja airbase, the neighbourhood of Celbi in Figueira da Foz, RTP-TV building in Av. 5 de Outubro and Instituto Superior Técnico, Lisbon.
The Number of employees rose up to 100 workforce.
1980
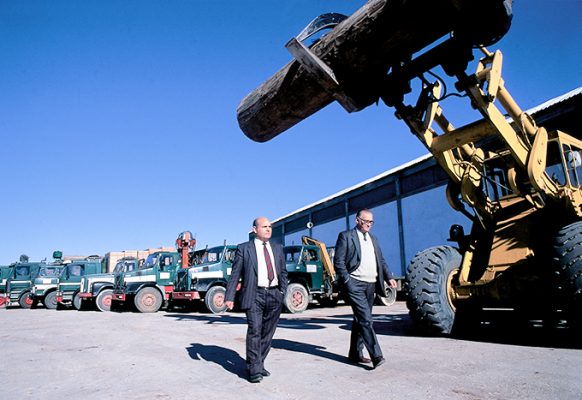
The 80’s: major investments
The growing credibility the company was gaining in the market, together with a professional administration, both have contributed to a new era of dynamic investment and business by mid-80’s. Rui Oliveira joined the commercial team as its leader and the company started to intensify its efforts on finding new foreign markets and exports began to flow into France, Spain, Germany, and even Japan,.
This was a glorious decade with the biggest investments the company had ever made!
1981
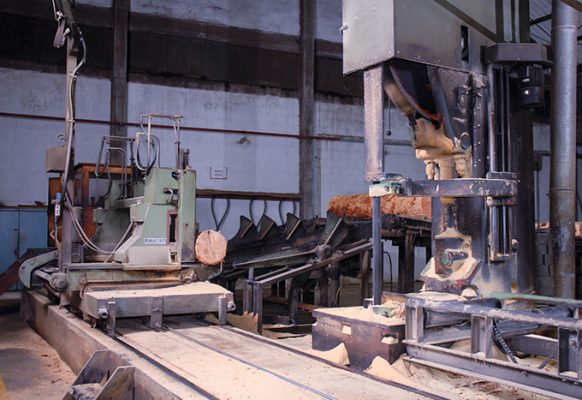
Growth
In order to increase capacity, new production units were built, and there was an investment in a modern sawmill for pine and exotic logs, new woodworking machines like: modern Veneer slicers, veneer dryers, jointing machines, boiling tanks, industrial scales, truck fleet and a wider logistic capacity.
Another big step was the introduction of a new Computerized management and communication system and the telefax has replaced the old Telex.
1987
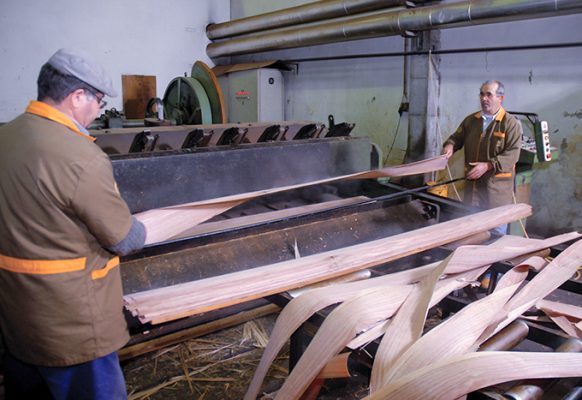
Wood Veneer
Beginning of the veneer production.
1987
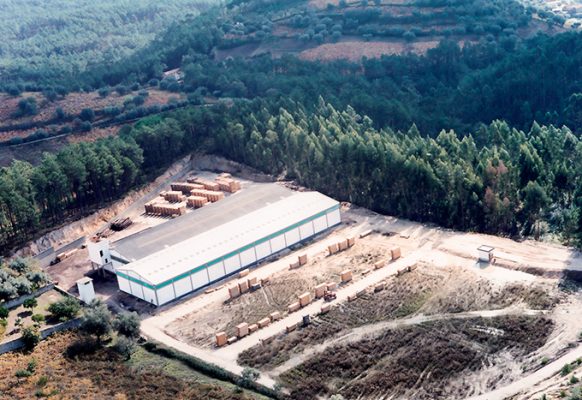
Emprimade
As a step forward with the new business atmosphere, Rui Oliveira joined also the Administration of the sister company Emprimade.
1987
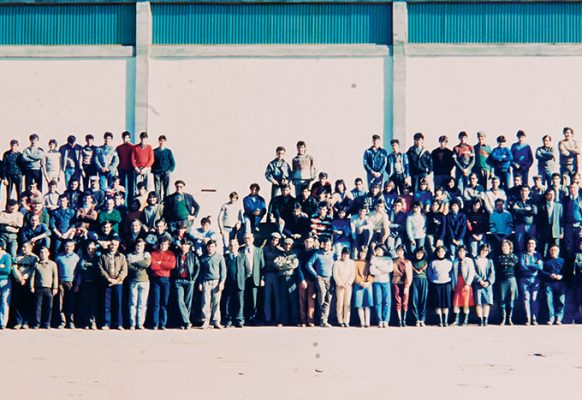
20% of exports
Valco staff were exceeding 130 and yearly turnover reached 1.7 million escudos – almost 20% of which were export.
1990
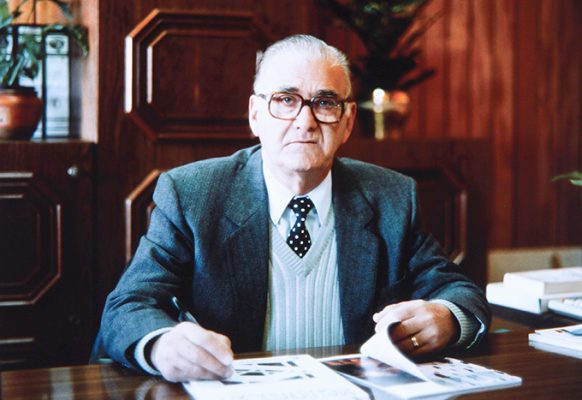
Administration stalemate
The early 90’s began with the death of Mr. Henrique Rodrigues, one of Valco’s stakeholders, on April 12nd 1990. This unexpected sad event has unfortunately originated some serious problems on the company’s regular management structure, due to a long conflict with heirs, which led to a stalemate decade of uncertainty and intense court lawsuits.
A deal could at last be found between both parties, and the company could then return to normal activity, concentrate on the business and restructure its administration board.
1991
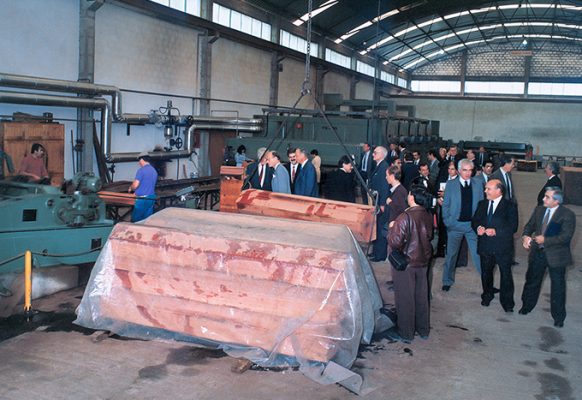
EFTA Award
EFTA award for outstanding merit.
1991
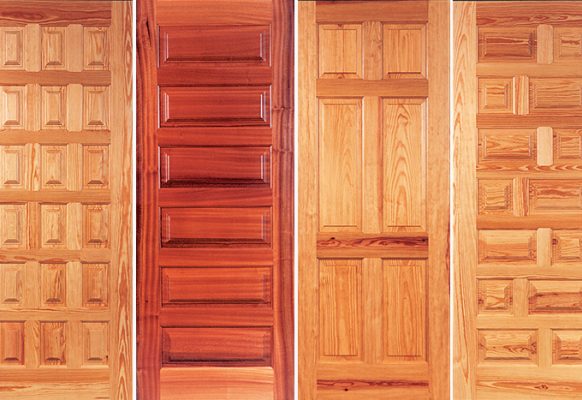
New Era
In spite of the existing constraints, Valco was able to keep focus on its core business: the production of doors, wardrobes, joinery and veneered panels. New integrated management programs were introduced, the company was connected to the internet, a new boiler, the acquisition of new CNC technology, and a state-of-the art finishing line were installed and we started with the production of glue-lam pine panels.
1991
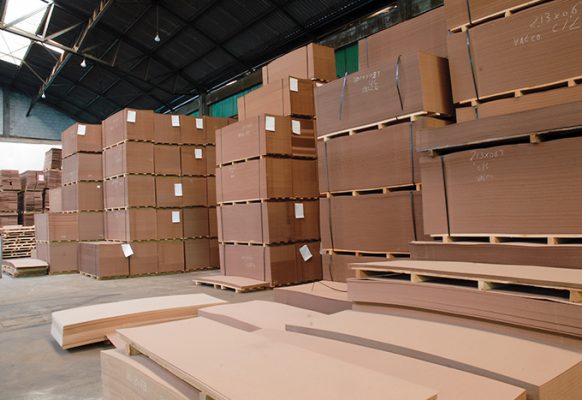
Internationalization Process
The Company consolidated the control of all phases of the production process: from forest management to the sawmill for pine and exotic lumber, veneer production, veneered panels, door line, joinery and finishing line.
Internationalization strategy: The domestic market had become too small and inadequate for Valco’s capacity, so we had to define and reinforce our strategy in foreign markets in order to cope with existing multiple business opportunities.
A business plan was established with the focus on trips to some different and somehow “unusual” countries like: Morocco, Egypt, Angola, Mozambique and Cape Verde and sales contracts were signed with these new markets.
1991
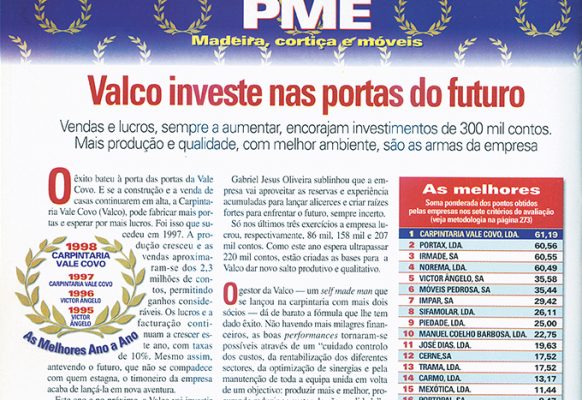
PME Prestígio - company’s MERIT AWARD
The company invested in a new production plant, 2 CNC profilers, 1 veneer jointing machine and 2 trucks. In 1994, 1997 and 1998, the company was awarded a PME prestige prize, for its outstanding results; however, due to existing Administration conflicts, Valco could not follow the economic growth of the market.
2003
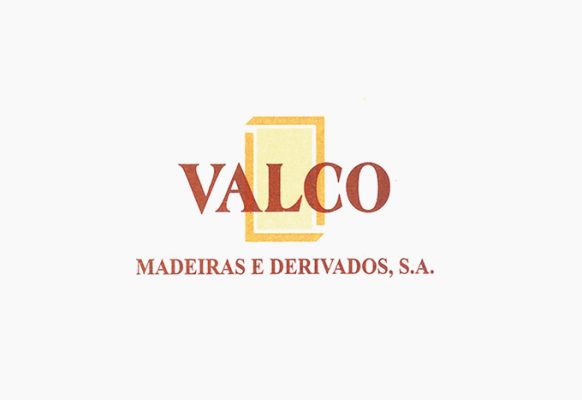
The new Valco corporation
Valco, s.a. was finally established as a PLC, with new share-holders.
2004
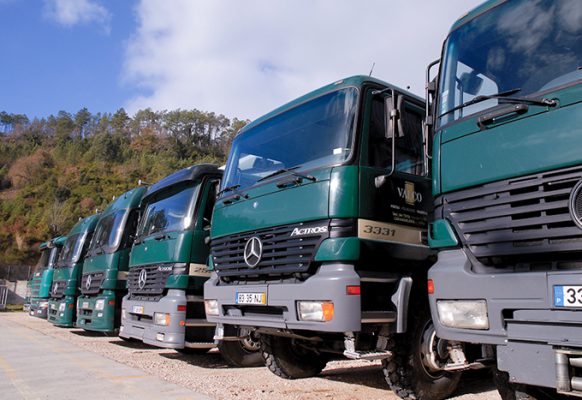
LogisticS reinforcement
New CNC machining centres for automated production lines for doors, frames and packaging, a new finishing line and the set up of a quality system ISO-9001. Logistics has been strengthened by the acquisition of heavy-duty vehicles.
2006
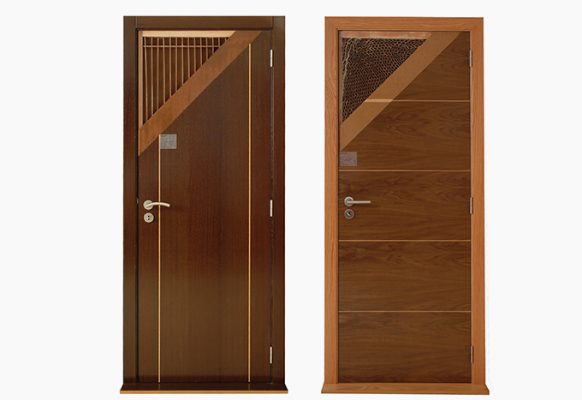
Ariporta®
As pioneers in standard production of doors and interior solutions, we pride ourselves to have kept up with the new market. We have therefore developed and patented a fully-finished doorset, with brand name “ARIPORTA”, which consists of a complete finished pre-hung or knock-down kit with: door leaf, frame, adjustable architrave and all hardware items ready to be installed on site.
2006
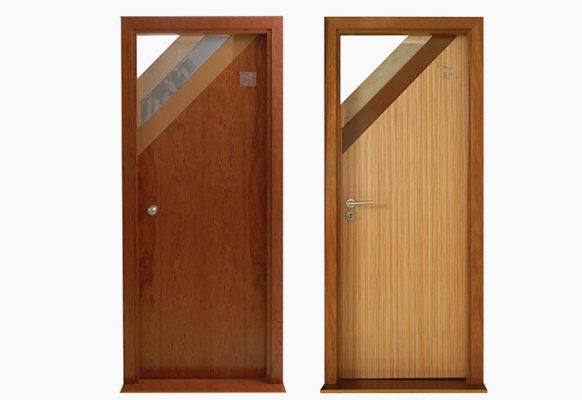
Certification
Certification of a wide range of products, such as: technical doors, wood, paneling, and environment, as a strategic response to the growing consumer demand for socially responsible products and suppliers.
2007
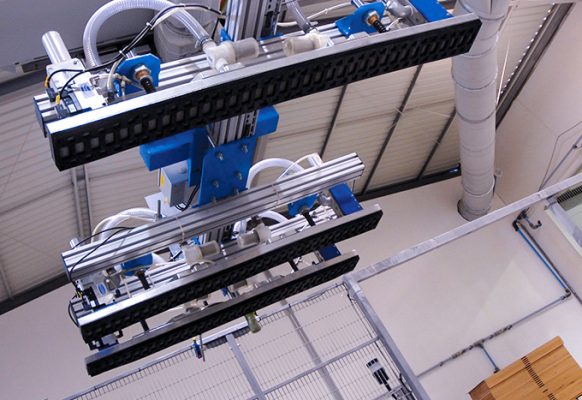
New automated roll pre-finishing line
2017: Acquisition of a New finishing line – an investment over 1,5 m€.
2007
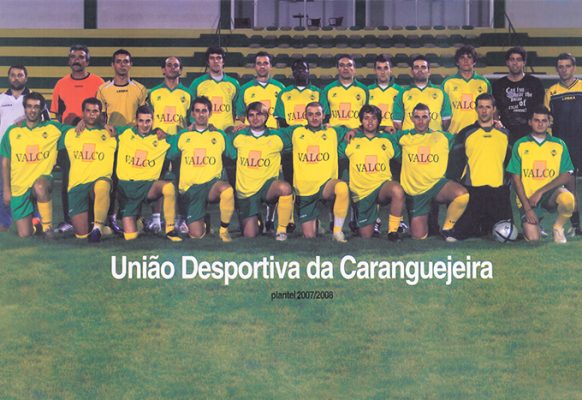
Active involvement and support of local social, cultural and sports associations
The founder of VALCO has always devoted a genuine concern and commitment with local community: football club, philharmonic band, nursing and day care centers and parish council.
2008
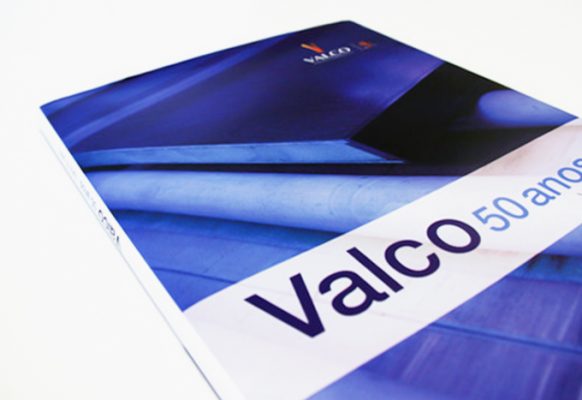
50 years celebration
To celebrate the 50th anniversary of the company set up a renovation plan of its office headquarters and showroom, renewal of the corporate branding, internet website, new paper and online catalogues, presence in trade fairs. The company also implemented a quality management system, as well as a Safety& Health programme at work.
2008
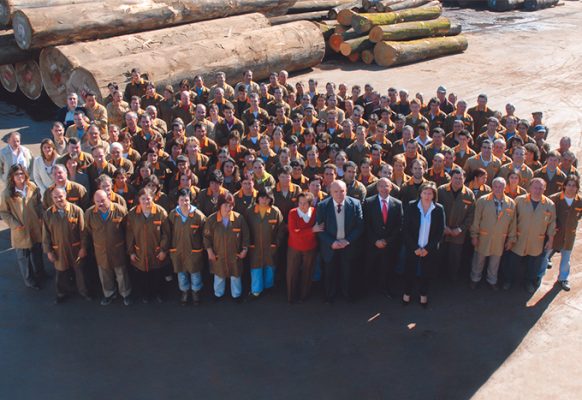
Largest private SME in Portugal
Valco’s facilities are the expression of a leading company in the wood sector, as the largest national SME door manufacturer. The factory covers abt. 65,000m2, employs 170, with an annual turnover of 16.5 million euros in 2007.
2008
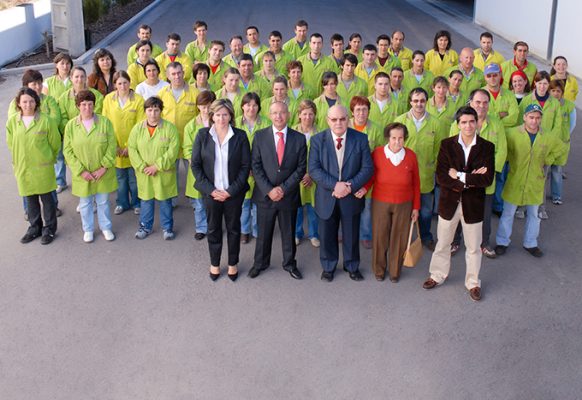
Production and trading of engineered moulded doors
Emprimade, our sister-company, has emerged as a major manufacturer of engineered moulded doors, with a turnover of 7.5 m€, and employing 65.
2008
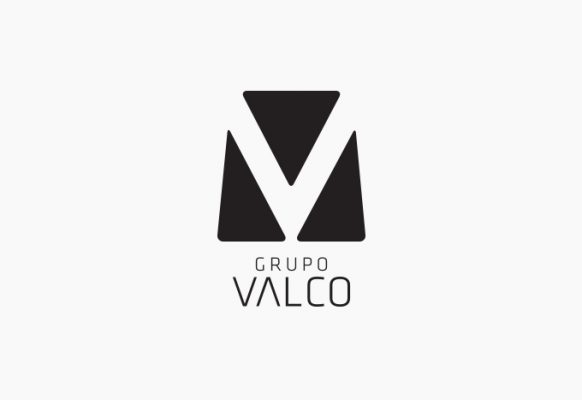
Group restructuring
Economic context at the time has led to a deep restructuring of the group, reallocating production and staff, in order to take full advantage of synergy between both Valco and Emprimade manufacturing sites and become much more competitive.
2009
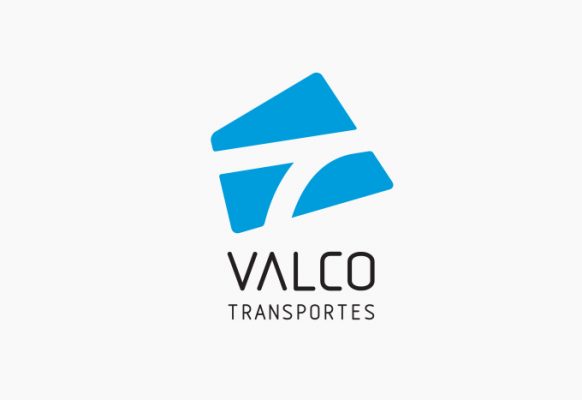
Valco Transport network
Valco Transport Firm was created in order to provide wider and more flexible logistic support to the production activity.
2012
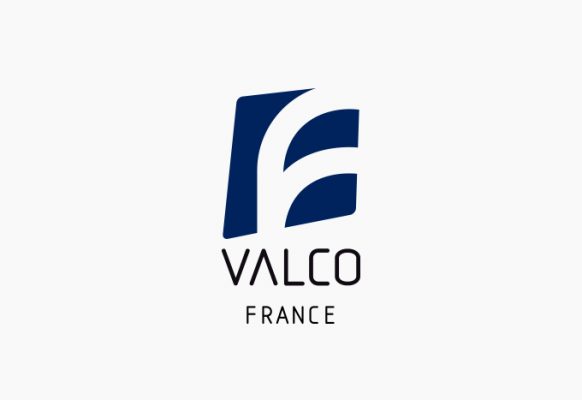
Valco France
The company created an international branch company, with office and warehouse facilities in France as “ S.A. Valco France ”
2013
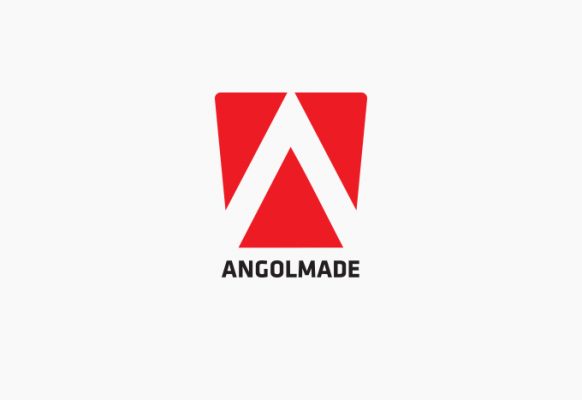
Valco in Luanda - ANGOLA
A nother branch office and a warehouse were opened in luanda, as “Angolmade, S.A.”
2014
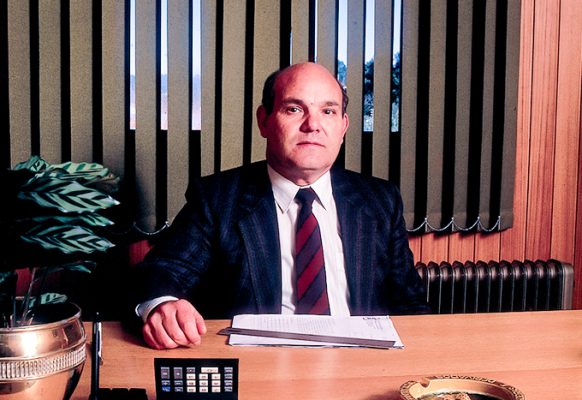
Founder Gabriel Oliveira
Company founder, Gabriel Oliveira passed away on April 17th, 2014.
2016
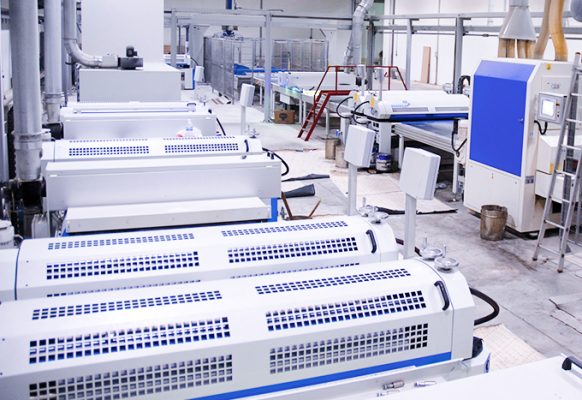
Restructure of the internal Logistics, warehousing and shipment sections
New investment in the logistics and shipment, as well as a new layout of DOORS, joinery and finishing lines.
2017
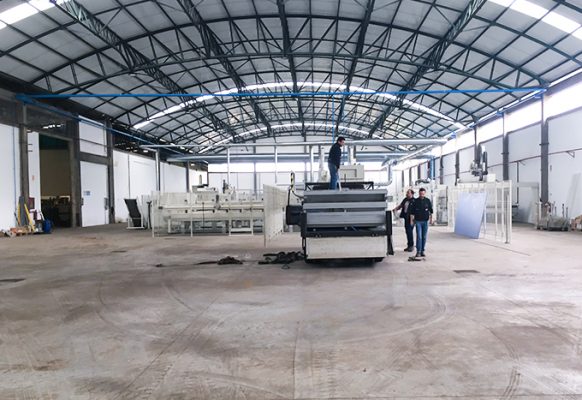
Automated line for cupboard&Wardrobe production
Acquisition and set up of a modern 4.0 line for wardrobe&cupboard production. This major investment includes: erection of a new industrial hall, new dust extraction system, compressed air and a new waste collector.
This year was severely hit by wildfires, with consequent raw material shortages of pine logs, which are vital for the normal sawmill activity.
2018
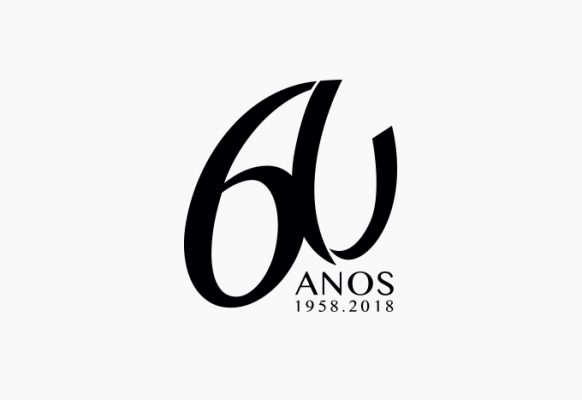
60 years
Valco Group celebrates its 60th anniversary.